by marketing | Dec 11, 2023
Robotics Engineer
Our Company:
At Stout we design, manufacture, and build machines for the agriculture industry. Our machines integrate artificial intelligence, machine vision and deep learning into smart agricultural tools.
Location: Salinas, CA
Salary Range: $110,000 – $190,000 per year
The Role: Our team is seeking a Robotics Engineer to shape the future of smart agricultural tools. In this pivotal role, you will be instrumental in designing and maintaining the electrical and controls systems for our advanced automated machinery. If you are passionate about pushing the boundaries of technology, contributing to the evolution of precision agriculture, and enjoy working on the cutting edge of electrical engineering and controls, Stout welcomes your expertise. Join us in a role where you can make a tangible impact on the intersection of technology and agriculture.
Areas of Responsibility:
- Design, develop, and maintain electrical and controls systems for automated machinery.
- Create electrical schematics and wire harness diagrams, working closely with electrical technicians on prototype development.
- Support deployed production systems through performance improvements and new functionality implementation.
- Follow best practices for controls and firmware engineering, including testing, issue tracking, code reviews, and post-deployment support.
- Participate in end-to-end system development, from design to implementation, deployment, and maintenance.
- Develop automated and manual test procedures and troubleshoot electrical circuits and control systems.
Preferred Qualifications:
- B.S. or equivalent in Electrical Engineering, Computer Science, or a related field.
- 5+ years of relevant work experience in circuit design and/or wire harness design, and controls or firmware development using C/C++.
- Working knowledge of electrohydraulic systems, including solenoids, valves, sensors, pumps, and motors.
- Experience with version control systems, continuous integration, and automated testing.
- Proficiency in electronics design tools such as Altium, Capital, Cadence, KiCad, etc.
Ideal candidate:
- Strong analytical and organizational skills with meticulous attention to detail.
- Proactive, self-motivated individual with a positive attitude.
- Effective problem-solving skills and the ability to troubleshoot and debug systems.
- Demonstrated ability to work independently and collaboratively in a team environment.
- Excellent time management, prioritization, and follow-up skills.
- Team player with a can-do attitude, promoting a positive company image and supporting manufacturing efforts.
- Honest, trustworthy, and respectful, with a commitment to confidentiality.
- Strong written and verbal interpersonal skills for effective communication.
by marketing | Oct 24, 2023
Yuma Innovation Showcase
THE EVENT:
Join us for an extraordinary event in the Winter Salad Bowl of the World that celebrates cutting-edge technology of our Smart Cultivator along with, other advancements coming down the pipeline. Our Yuma Innovation Showcase is set to be a remarkable educational showcase for agricultural innovation. The spotlight will be share with our parent company, Tanimura & Antle, along with our sister companies, PlantTape, and 3 Star Lettuce.
Where: Tanimura & Antle | Yuma, Arizona
When: Monday, November 27th – Friday, December 1st
WHY ATTEND?
Stout has been a trailblazer in pioneering innovative farming solutions through AI. As a leader in the ag tech space, we are revolutionizing the way we approach crop management and data analytics in agriculture. Their innovative technologies are designed to maximize yield, minimize waste, and enhance the overall efficiency of farming operations. Come and explore how our solutions are transforming the landscape of modern agriculture.
WHAT TO EXPECT:
Tanimura & Antle has been at the forefront of sustainable and innovative farming practices. As leaders in the agriculture industry, we are committed to nurturing an environment of continuous improvement, and we proudly present this event to our valued customers as a testament to our dedication to innovation and commitment to doing what it takes to provide our premium fresh produce for the years to come.
PlantTape has reimagined transplanting techniques with their state-of-the-art automated transplanting system. This cutting-edge technology streamlines the planting process, significantly reducing labor costs and enhancing crop uniformity. Witness the future of planting as PlantTape showcases their latest innovations, a light-weight transplanter developed for small scale farmers or as an option for larger growers to plant in wet conditions as well as their new tomato automated transplanter.
3 Star Lettuce is at the forefront of the lettuce seed industry, pioneering innovative research and development and environmentally conscious practices that ensure high-quality, disease-resistant, flavorful and resilient seed varieties. Their dedication to producing superior lettuce seeds makes them a driving force in lettuce farming. Visit 3 Star to see the next generation of lettuce varieties first hand.
by marketing | Sep 14, 2023
SALINAS, CA. (September 5th, 2023) – Stout Industrial Technology, a leading pioneer in agricultural technology, is excited to announce its participation at this year’s prestigious International Forum for Agricultural Robotics (FIRA USA). The event will take place from September 19-21, 2023, at the Salinas Sports Complex in Salinas, CA, and will bring together industry leaders, experts, and enthusiasts in the field of agricultural robotics.
As a company that is revolutionizing the agricultural industry through cutting-edge AI technology and automation solutions, Stout Industrial Technology is thrilled to showcase its latest advancements and to foster connections with prospective customers and industry professionals at FIRA USA. The event provides an excellent platform for the company to demonstrate how its innovative technology is shaping the future of agriculture.
Attendees will have a variety of opportunities to engage with the Stout team and see the Smart Cultivator, an automated AI-powered weeder and cultivator, in action. The Stout team will partake in an Inno’Pitch session on September 20th, at 4:00 p.m. During this session, attendees can expect a 15-minute presentation followed by a dedicated and interactive Q&A session with the Stout team.
There will be two demonstrations where the Stout Smart Cultivator will operate in a romaine field for attendees to watch the machine in action. The demonstrations are scheduled for September 20th, at 10:15 a.m. and again on September 21st, at 2:00 p.m. Throughout the demonstration, attendees will have the opportunity to interact with Stout’s state-of-the-art Smart Cultivator. The Stout Industrial Technology team will be on-site, providing valuable insights and explanations about the machine’s capabilities, highlighting the company’s commitment to improving efficiency, productivity, and sustainability in critical labor heavy farming practices such as weeding and cultivating.
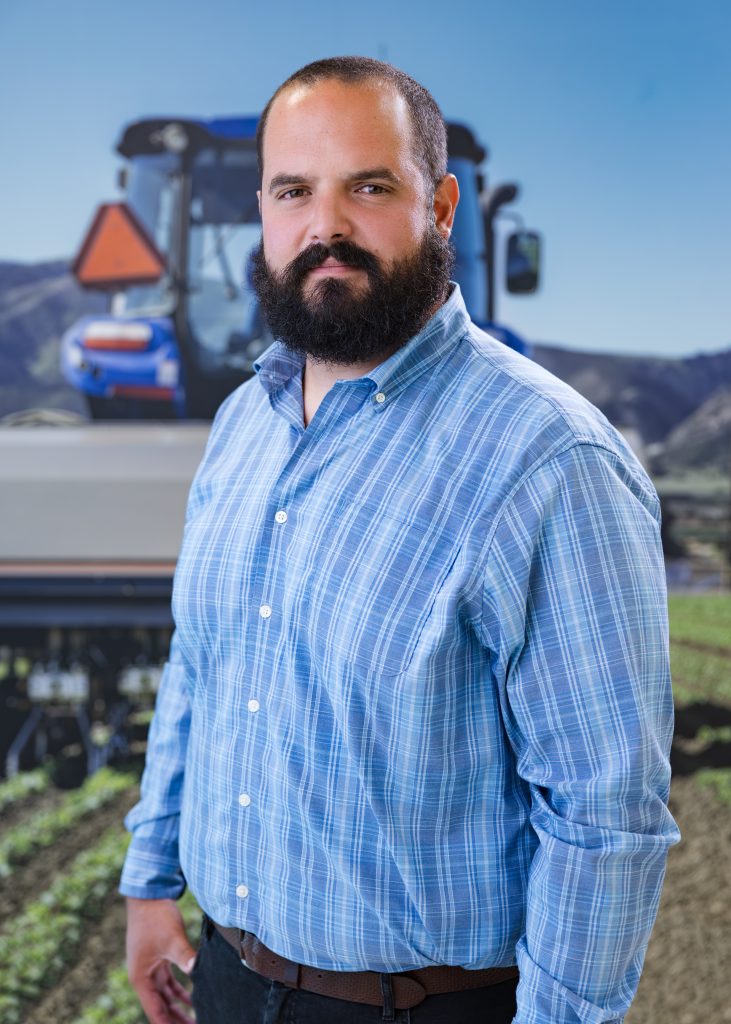
Ryan Mazzuca, Director of Business Development
“We are thrilled to be a part of this year’s FIRA USA and to showcase our Smart Cultivator machine that leverages our proprietary True Vision™ AI technology,” said Ryan Mazzuca, Director of Business Development at Stout Industrial Technology. “This event presents a unique opportunity for us and innovative growers alike to connect with industry leaders, exchange insights, and explore partnerships that will drive the future of agriculture.”
FIRA USA is widely recognized as a premier event for autonomous and robotic farming solutions, with a comprehensive program featuring expert speakers, panel discussions, and networking opportunities. Attendees stand to will gain valuable insights into the latest trends, challenges, and opportunities in the field, as well as witness live demonstrations of cutting-edge technologies.
Stout Industrial Technology invites all attendees to visit their booth #53 to learn more about the transformative technology of their Smart Cultivator and discover how it can minimize labor costs and increase farming efficiencies.
by marketing | Aug 4, 2023
Stout Industrial Technology Appoints New Leadership
SALINAS, CA (August 3rd, 2023)
Stout Industrial Technology, a prominent AI company focused on agtech solutions, is proud to announce two significant additions to its leadership team. Ryan Mazzuca joins as the new Business Development Director, and Lance Portman takes the helm as CEO. These strategic appointments are geared towards reinforcing Stout’s commitment to continued growth and enhancing its position as an industry leader in artificial intelligence and agricultural technology.
“I am looking forward to leading the innovative team at Stout,” said Portman. “Together, we will build upon Stout’s already impressive accomplishments and drive the company’s growth to even greater heights. Stout’s commitment to revolutionizing agriculture and supporting farmers is unwavering, and I am excited to be a part of this transformative journey.”
Portman brings a distinguished leadership background and record of successfully bringing products to market, stewarding innovative teams and constructing sound business practices, having held key executive roles at prominent companies across the globe, including BJ Services Company, Baker Hughes Incorporated, and PlantTape, a fully automated agriculture transplanting system. His extensive experience in managing diverse operations, specifically in the agricultural sector, will be invaluable in driving Stout’s mission to provide growers with durable, labor-saving farm solutions.
Mazzuca joins Stout as the new Business Development Director, bringing a wealth of experience from companies such as Bloomfield Robotics, Iron Ox, and Tanimura & Antle. His proven track record in identifying and cultivating strategic partnerships will play a pivotal role in expanding Stout’s market reach and solidifying its position in the industry.
“I am deeply honored to be a part of the talented, visionary team at Stout,” remarked Mazzuca. “Stout has already established an exceptional product that is positioned to shape the future of agriculture. I am looking forward to contributing to the team and supporting growers tackling the adoption of Stout’s cutting-edge technology.”
With a steadfast commitment to agricultural innovation and a focus on developing AI solutions that empower growers, the Stout team continues to lead the charge in shaping the future of farming. The recent additions to the team are expected to contribute significantly to their ongoing success, further solidifying Stout’s position as the leader for AI solutions in the agriculture industry.
by marketing | Dec 9, 2022
Stout Industrial Technology Adds Global Distribution And Investment From CNH Industrial
Helping growers automate labor-intensive field work with artificial intelligence
SALINAS, CA (December 9, 2022)
Stout Industrial Technology, Inc. (Stout) has announced an investment from and global distribution agreement with CNH Industrial that will see Stout’s AI-powered Smart Cultivators sold and serviced at New Holland dealerships worldwide.
The machines simultaneously cultivate and remove weeds at the rate of 1 – 2 acres per hour and are anticipated to be available for sale at selected New Holland dealers in early 2023. Stout currently has Smart Cultivators operating in locations across the US and in the United Kingdom.
The minority investment by CNH Industrial adds Michele Lombardi to Stout’s Board of Directors and adds Stout’s proprietary vision system, neural network and AI expertise to CNH Industrial’s See & Act portfolio of products.
Stout Industrial Technology is a Salinas, CA based artificial intelligence company focusing on labor-intensive applications in agriculture. The Company builds software-defined implements for tractors that use machine vision and AI to identify and remove weeds via mechanical actuation instead of chemicals. Born inside a grower-shipper operation, Stout’s hardware and software solutions are developed from the grower’s perspective, hardened in the field prior to commercialization and continuously improved to help growers lower their operating costs and increase their margins.
Learn more at www.stout.ai or follow Stout Industrial Technology on LinkedIn.
CNH Industrial (NYSE: CNHI / MI: CNHI) is a world-class equipment and services company. Driven by its purpose of Breaking New Ground, which centers on Innovation, Sustainability and Productivity, the Company provides the strategic direction, R&D capabilities, and investments that enable the success of its global and regional Brands. Globally, Case IH and New Holland Agriculture supply 360° agriculture applications from machines to implements and the digital technologies that enhance them.
Across a history spanning over two centuries, CNH Industrial has always been a pioneer in its sectors and continues to passionately innovate and drive customer efficiency and success. As a truly global company, CNH Industrial’s 37,000+ employees form part of a diverse and inclusive workplace, focused on empowering customers to grow, and build, a better world.
For more information and the latest financial and sustainability reports visit: cnhindustrial.com
For news from CNH Industrial and its Brands visit: media.cnhindustrial.com